G Force 375 Platinum Incl Crack

Recently, a mechanical crack-based strain sensor with high sensitivity was proposed by producing free cracks via bending metal coated film with a known curvature. To further enhance sensitivity and controllability, a guided crack formation is needed. Herein, we demonstrate such a ultra-sensitive sensor based on the guided formation of straight mechanical cracks.
The sensor has patterned holes on the surface of the device, which concentrate the stress near patterned holes leading to generate uniform cracks connecting the holes throughout the surface. We found that such a guided straight crack formation resulted in an exponential dependence of the resistance against the strain, overriding known linear or power law dependences. Consequently, the sensors are highly sensitive to pressure (with a sensitivity of over 1 × 10 5 at pressures of 8–9.5 kPa range) as well as strain (with a gauge factor of over 2 × 10 6 at strains of 0–10% range).
This calculation agrees very well with established barrel times as. In my personal opinion I think the average G force is probably the.375 NE 2½, 0.38, 32000, 510. Tip is accelerated to the speed of sound and the crack is a sonic boom. Platinum Offline. Joined Oct 2006; Posts 3442; EE Offline. G-Force 3.7.5 Platinum With Crack 9 download locations. G-Force_375_Platinum.exe 4 MB; ReadMe.txt 0 MB; Torrent downloaded from Demonoid.com.txt 0 MB.
Attestaciya starshego vospitatelya dou samoanaliz. A new theoretical model for the guided crack system has been suggested to be in a good agreement with experiments. Durability and reproducibility have been also confirmed. Studies on wearable healthcare and artificial electronic skin devices,,, and the development of high performance sensors are attracting profound interests. Various types of pressure sensors have been developed based on nanowires,, silicon rubber, piezoelectric, and organic thin-film transistors, for accumulating external information. Also, strain sensors based on carbon nanotubes,, nanofibres, graphene platelets and mechanical cracks,, were reported. Although cracks were considered as defects to be avoided in general, studies on cracks such as patterning by cracks, thin-film cracking for producing nanowires, and interconnectors, have been reported recently. A crack sensor inspired by the spider’s sensory system was reported to be remarkably sensitive to strain and vibration.
However, it has limitations in which strains of merely 2% can be applied. The cracks in Ref. Comprised a system of parallel cracks which revealed a universal behavior of the resistance against the strain which was close to a power-law dependence (see below). Yet, more control over the crack morphology and stretchability is still required for alternating the sensor into a more stretchable one for pressure sensing. Properly designed crack lip morphology can provide the rapid increase in the resistance with the strain and thus in sensitivity.
Cracks should be made straight with negligible asperity that may give sharp lip disconnection and rapid increase in the resistance vs strain. In this work, we designed a micro-patterned crack sensor and demonstrated its ultrahigh sensitivity to external forces (e.g.
Pressure) and physiological signals (e.g., wrist pulse). An illustration of the patterned crack-sensor is presented in. We deposited stiff metal layers (first chromium 10 nm, then platinum 20 nm) on the top of a hole-patterned C-polyurethane acrylate (C-PUA) (details are in the and ). Then, 10% strain was applied to a rectangular shape sample along both grid directions one by one for crack formation. The lateral dimension of the sensor strip was 5 mm × 10 mm on the 100-μm-thick C-PUA as shown in.
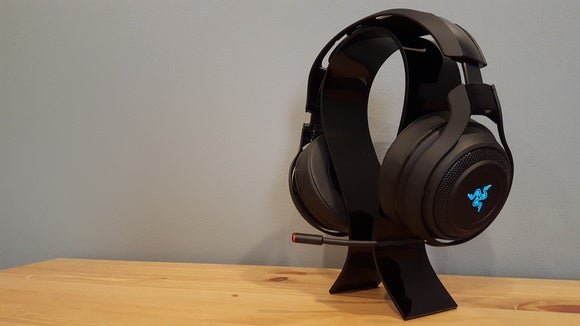
In terms of the stretchability, the crack sensor can be stretched by 10% strain as shown in the photograph in. Hole-patterns generate stress concentration between adjacent two holes and induce regular cracks as shown in. When stretching force is applied to the patterned crack sensor, cracks formed perpendicular to the force are opened (red arrows) while the parallel ones are closed (blue arrows) because the Poisson’s ratio of rubber-like C-PUA induces such a behavior as shown in. After preparing the crack network, the sensor undergoes the strain test. Before applying strain cracks are closed tightly as shown in. After stretching the contact area between crack lips decrease as shown in thus increasing the electrical resistance that was measured.